SLATE & TILE ROOFING INSTALLATION & REPAIR
SLATE ROOFING COMPANY SERVING NJ FOR 17 YEARS
Since 2006, Pfister Adore Construction has offered the highest quality workmanship and unmatched level of expertise in specialty slate roofing. Looking for ‘slate roof repair near me’? Retain the historic beauty and strength of your slate roof by carefully selecting craftsmen to repair your roof with the same skill and techniques originally designed and keep […]
Since 2006, Pfister Adore Construction has offered the highest quality workmanship and unmatched level of expertise in specialty slate roofing.
Looking for ‘slate roof repair near me’? Retain the historic beauty and strength of your slate roof by carefully selecting craftsmen to repair your roof with the same skill and techniques originally designed and keep your roof alive for hundreds of years. Adore Construction never uses tar or other poor substitutes for repairs as they are unsightly and ineffective against leak prevention while damaging the slates. We offer the following roofing services:
- Residential & Commercial Slate/Tile Roof Design & Installation
- Residential & Commercial Slate/Tile Roof Repair
- Residential & Commercial Slate/Tile Historic Roof Repair
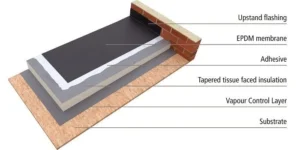
FLAT ROOFING SYSTEM
EPDM Roofs – The No. 1 Choice for Flat Roofing Applications
Info Courtesy of EPDM Roofing Association
The EPDM (ethylene propylene diene terpolymer) single-ply rubber roofing membrane has been an appealing choice for the low-slope commercial roofing industry for over 40 years.
- The number one roofing choiceof architects, roof consultants and contractors for both new construction and replacement roofing projects according to Building Design and Construction magazine and the National Roofing Contractors Association (NRCA) 2002-2003 market surveys.
- Over 1 billion square feetof new roof coverings in the United States annually
- More than 500,000 warrantyroof installations on 20 billion-plus square feet
SUPERIOR PERFORMANCE
The greatest test of any construction material is how it performs under actual field conditions. Forty years of empirical experience in field applications has shown EPDM to have the roofing industry’s longest average service life. Characteristics that contribute to this superior overall system performance include:
- Cyclical membrane fatigue resistance
- Proven hail resistance
- High resistance to ozone, weathering, and abrasion
- Flexibility in low temperatures
- Superior resistance to extreme heat and fire
- Thermal shock durability
- Ultraviolet radiation resistance
EPDM’s high resistance to wind damage has also proven to be an increasingly desirable attribute. These roof systems can be designed to meet a variety of wind uplift criteria from Factory Mutual, including 1-60, 1-90, and 1-120 ratings and greater, and the stringent code of Dade County, Florida. Architects, roof consultants and contractors have come to depend on EPDM’s time tested, long-term performance.
Environmental Responsiveness
EPDM is one of the most sustainable and environmentally responsible roofing materials used today in the construction industry. Its successful track record of superior overall system performance results in low life cycle costs. Less frequent replacement results in decreased building disruptions and reduced impact on the environment. The initial production of the membrane has a low-embodied energy number (the amount of energy required to produce and implement a product from material extraction, manufacturing, and installation).
For designs requiring a colored surface, an Energy Star approved coating can be applied. The EPDM surface allows for a robust bond with the coating that results in long-term performance. EPDM also has high emissivity (the percentage of absorbed energy a material can radiate away from itself). This high emissivity allows the heat energy to be reflected into the atmosphere instead of being absorbed by the building. As a result, a building can “cool off” faster at night, rather than hold the heat.
Low VOC/VOC free products are also available. VOC (Volatile Organic Compounds) are a factor in creating air pollution.
Numerous manufacturing facilities, locally experienced installation crews and systems that perform well in conditions of high thermal value all allow for Leadership in Energy and Environmental Design (LEED) point possibilities. In fact, the Green Building Digest’s Issue No. 14 lists EPDM as a ‘Best Buy’ for low-slope roofing. For those systems that have reached the end of their service lives, EPDM membranes are recycled to become walkway pads or used for other purposes.
FREQUENTLY ASKED QUESTION
- What is EPDM?
- What does EPDM look like?
- How can the performance of EPDM be gauged over the last 40 years?
- How does the performance of EPDM membrane compare to built-up roofing?
- What is the maximum size sheet for EPDM membrane?
- What is the difference between black EPDM and white EPDM membrane?
- Can EPDM membrane be used in roof top garden applications?
- Does EPDM require systematic maintenance or additional coatings or treatment to achieve its life expectancy?
- Are temperature limitations associated with the installation of EPDM roofing system?
- Is the performance of the EPDM membrane adversely affected geographically due to temperature extremes?
- Is EPDM environmentally beneficial?
- What is the expected longevity of EPDM membrane?
- Can EPDM be coated or painted?
- Can EPDM be used in installations other than roofing?
- Generally speaking, is an EPDM single-ply membrane roofing system cost effective?
- How long can an EPDM roofing system be warranted?
- How popular is EPDM single-ply membrane?
- Would repairs to an EPDM membrane be impaired by aging?
- What is EPDM?
EPDM is an elastomeric compound that is manufactured from ethylene, propylene, and a small amount of diene monomer. These ingredients are synthesized to produce a product that exhibits a high degree of ozone, ultraviolet, weathering and abrasion resistance, and outstanding low temperature flexibility. These ingredients also contribute to resistance to acids, alkalis, and oxygenated solvents (i.e., ketones, esters, and alcohols).
- What does EPDM look like?
Black EPDM has a smooth surface like natural gray slate and does not contain surface granules that can eventually be lost on other materials.
- How can the performance of EPDM be gauged over the last 40 years?
With over 1 billion square feet of membrane installed worldwide, EPDM has established itself as the membrane for all climatic conditions. This is supported by various laboratory studies and actual field installations. This excellent track record is the result of unique and unmatched physical characteristics:
- EPDM has superior resistance to UV (ultraviolet) radiation.
- EPDM has unmatched resistance to thermal shock.
- EPDM exhibits superior resistance to cyclic fatigue.
- EPDM has superior resistance to hail damage.
- EPDM will not become brittle and will not shatter due to low temperature flexibility.
- How does the performance of EPDM membrane compare to built-up roofing?
Expansion and contraction, ponding, moisture, thermal shock, and temperature extremes are all factors that promote premature degradation of a roofing membrane. The great elongation and low temperature flexibility of EPDM membrane accommodate building movement in various climatic conditions without stressing the material. Its moisture absorption resistance allows the material to be installed in assemblies with lesser slope than other single-plies and makes it tolerable to incidental ponding and deflection. Unlike built-up roofing, EPDM membrane does not contain organic material that can decay as the result of moisture caused by condensation or leaks. EPDM membrane, due to its ability to withstand extreme temperatures, can be successfully used in assemblies with greater thermal resistance (thicker insulations with higher R-values). The ability of a roofing membrane to withstand temperature extremes is an important trait of a high-performance material because temperature extremes could promote premature membrane aging and reduce the life expectancy of a roof.
- What is the maximum size sheet for EPDM membrane?
Sheets as large as 50 feet in width are produced mostly for use in ballasted and mechanically fastened applications. Narrower widths are also produced to offer applicators greater flexibility in positioning membrane.
Narrower sheets are also produced without factory seams (seamless) for use primarily in adhered and mechanically fastened applications. The major advantage of seamless material is the elimination of factory splice T-joints that occur when factory seams intersect with field splices. This reduction in T-joints significantly increases the potential for watertight performance by eliminating potential “water channels” into field splices.Both narrow and wide sheets are manufactured in varying lengths from 50′ to 200′.
- What is the difference between black EPDM and white EPDM membrane?
In addition to the oils and the polymers used to make an EPDM membrane, another ingredient is added to the mix to enhance UV resistance. In the case of a black membrane, carbon black is added, which converts UV rays into heat. With a white membrane, in lieu of carbon black, titanium dioxide is typically used to reflect UV rays and prevent it from attacking the polymer.
- Can EPDM membrane be used in roof top garden applications?
EPDM has a proven track record in various waterproofing and pond lining applications which somewhat resemble roof top applications. However, there are certain rules that should be followed when designing a roof top garden regardless of the type of membrane used:
- Select a membrane with high puncture resistance.
- Establish redundancy in the waterproofing assembly by overlaying splices.
- Design the assembly to provide slope and proper drainage at the membrane level.
- Incorporate protection above the membrane to aid against root growth and possible puncture.
- Incorporate a drainage layer and a root barrier to influence root growth away from membrane.
- Select proper growth media for the type of roof garden intended.
- Does EPDM require systematic maintenance or additional coatings or treatment to achieve its life expectancy?
No. No special coating or other surface treatment is required. General maintenance in the form of good housekeeping should periodically be performed to remove debris and leaves, and to investigate the performance of other components.
- Are temperature limitations associated with the installation of EPDM roofing system?
In accordance with ASTM standard D 746, EPDM membrane has a brittleness temperature of -49ºF. While the membrane will remain flexible and pliable in extremely cold temperatures, adhesives, flashings, and tapes should be kept at room temperature (hot boxes are usually used on the rooftop to rotate adhesive cans and rolls of flashing). Although roofing contractors may select not to work in sub-freezing temperatures due to safety concerns, many EPDM installations have taken place in temps below 20ºF.
- Is the performance of the EPDM membrane adversely affected geographically due to temperature extremes?
In laboratory testing EPDM is subject to the most severe heat aging where samples are subjected to temperatures of 240ºF for 4 weeks. Also, in several studies field samples were collected from various geographic locations after years of exposure and in both cases (laboratory and field), the physical properties of the samples exceeded the original ASTM specification. Presently, there are numerous EPDM installations throughout colder regions in the U.S. (i.e., Alaska, Minnesota) as well as in the hot and humid climates of southern Florida and Texas. For the past 25 years, EPDM has been the roofing membrane of choice for many commercial and manufacturing facilities internationally. The material will not shatter in extreme, cold temperatures and remains flexible under severe thermal shock such as in dessert areas where evenings are extremely cold and days extremely hot.
- Is EPDM environmentally beneficial?
EPDM is one of the most sustainable and environmental materials used today in the construction industry. Its excellent performance transfers to low life cycle costs and less impact on the environment.
The initial production of the membrane has a low embodied energy number (the amount of energy required to produce and implement a product from material extraction, manufacture, and installation). In addition, several other components (such as cleaners, primers and adhesives) were developed for use with the EPDM membrane to reduce VOC (Volatile Organic Compounds) emissions during installation.
Post-industrial products can be reincorporated (recycled) into the manufacturing of other roofing products and accessories (i.e., walkways and roofing tiles), thus minimizing the impact on landfills.
- What is the expected longevity of EPDM membrane?
With many EPDM installations exceeding 40 years of exposure in the field under various climatic conditions, none of the material tested has shown alarming signs of degradation. Even though it would be difficult to predict, studies have shown aged EPDM membrane as having a potential life expectancy of 50 years
- Can EPDM be coated or painted?
Acrylic coatings are available that can be applied directly to a prepared EPDM surface. Preparation usually consists of cleaning the EPDM with a pressure washer and a detergent solution or wash. Latex-based paint products can also be used; however, the EPDM manufacturer should be contacted prior to application to ensure compatibility and continuation of warranty coverage
- Can EPDM be used in installations other than roofing?
Yes. EPDM has been used in various installations such as pond liners, tunnels, foundations, thru-wall flashings, terraces, garden roofs, and RV roofs.
- Generally speaking, is an EPDM single-ply membrane roofing system cost effective?
Dollar-for-dollar, EPDM roofing systems are the greatest value in the low slope commercial roofing industry. While installation costs vary from system to system as well as from building to building, generally, ballasted roofing systems have the lowest installed cost per square foot followed by mechanically fastened and fully adhered systems.
- How long can an EPDM roofing system be warranted?
Generally speaking, system warranties that cover material and labor costs are available; and different manufacturers offer various assemblies with standard warranties that vary from 5 and 10 to 15 and 20 years. In addition, premium coverage up to 30 years is available and can include coverage for higher wind speeds, incidental puncture, and hail resistance.
- How popular is EPDM single-ply membrane?
Within the United States, EPDM accounts for over 1 billion square feet of new roofing annually and represents approximately 35% of the entire roofing market. In Europe the market share is around 12% and growing. While it is difficult to predict percentages in other markets, accelerated growth is reported in the Middle East and China as well.
- Would repairs to an EPDM membrane be impaired by aging?
No. One of the most unique attributes of EPDM is its ability to be easily repaired as well as its potential for restoration unparalleled in the roofing industry. The characteristics of the membrane are such that, even after years of field service and exposure to the elements, repairs and/or modifications, such as the installation of a new rooftop unit, can be accomplished with ease and with the expectation of long-term performance.
Unlike other roofing systems that degrade or become brittle over time due to UV exposure, EPDM single-ply membrane maintains its integrity and flexibility. This allows for modifications as easy as washing the membrane, preparing the roofing membrane surface, adhesive applications, and the installation of new material.
